When it comes to metalworking, achieving a smooth, shiny, and flawless surface is often a key requirement, whether for aesthetic purposes or to improve the functionality of a metal piece. The process of metal polishing and finishing plays a vital role in transforming rough, dull, and imperfect metal surfaces into pristine, polished works of art or high-performance components. This is where metal polishing equipment and finishing compounds come into play. These tools and compounds are essential for achieving that professional finish and are widely used across various industries, including automotive, jewelry, aerospace, and manufacturing.
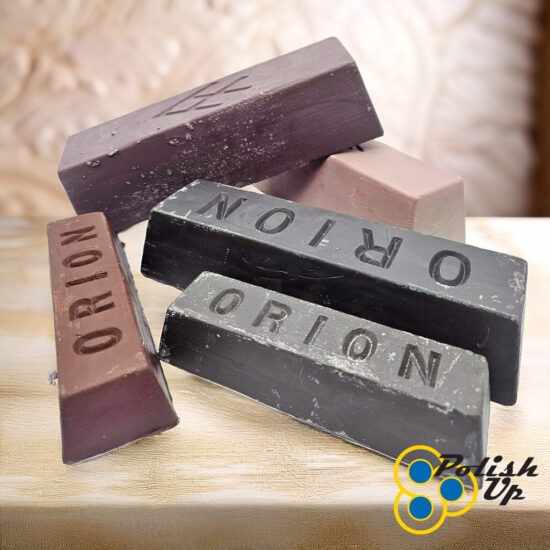
Metal Polishing Equipment: Tools for Achieving a Flawless Finish
Metal polishing involves the use of specialized equipment designed to smooth out rough surfaces, remove scratches, and restore a lustrous, reflective finish to metal. The type of equipment used depends on the metal type, desired finish, and the scale of the project.
1. Types of Metal Polishing Equipment
Polishing Machines: These machines are designed to hold polishing wheels and buffs, which rotate at high speeds to polish metal surfaces. There are various types of polishing machines, including:
Bench Polishing Machines: Compact and versatile, these machines are ideal for smaller items like jewelry, silverware, and decorative metal pieces.
Industrial Polishing Machines: These are larger, more powerful machines used for polishing large metal components, such as automotive parts or heavy machinery.
Polishing Wheels: Polishing wheels come in various materials, including cotton, felt, and sisal, and are used with polishing machines to provide a fine finish. The choice of wheel depends on the material being polished and the desired surface finish.
Cotton Wheels: Soft and absorbent, cotton wheels are often used for delicate polishing tasks.
Sisal Wheels: More aggressive than cotton, sisal wheels are ideal for removing rust and deep scratches from metals.
Rotary Tools: For smaller, more intricate jobs, a rotary tool with interchangeable attachments (like polishing pads or buffing wheels) can be highly effective. These tools are perfect for polishing jewelry, small metal parts, and intricate details that larger machines cannot handle.
Vibratory Tumblers: These machines are often used in industrial settings where high-volume polishing is needed. They use vibrational motion to polish multiple metal parts at once. The parts are placed in a rotating drum along with polishing media (abrasive materials), which gently smooths and polishes the surface.
2. How Metal Polishing Equipment Works
Metal polishing equipment typically works through a combination of mechanical motion, abrasive materials, and polishing compounds. The machine rotates the polishing wheel or disc at high speeds, and the abrasive compounds applied to the wheel's surface act as the key agents for smoothing out imperfections, scratches, and blemishes. The abrasive action combined with the polishing wheel’s soft material allows for the gradual reduction of rough surfaces, leaving behind a glossy finish.
Polishing machines can be operated manually or automatically, depending on the specific needs of the project. In large-scale applications, automated polishing machines can handle continuous processes, significantly increasing efficiency and productivity.
Finishing Compounds for Metal: Enhancing the Surface Quality
Once the metal surface is smoothed and polished, the application of Finishing compounds for metal takes the process to the next level. These compounds are essential in giving the metal a refined, mirror-like shine while providing added protection and improving corrosion resistance.
1. Types of Finishing Compounds
Finishing compounds are generally abrasive pastes, powders, or liquids that are applied to the metal surface during the polishing process. These compounds are designed to help refine the finish, remove any micro-scratches, and leave behind a smooth, shiny surface.
Buffing Compounds: These are applied to polishing wheels and are used to provide the final shine to metal surfaces. Buffing compounds come in different colors and grades:
White Buffing Compounds: These are mild abrasives that are perfect for softer metals like aluminum, brass, and silver.
Brown and Red Buffing Compounds: These are more aggressive abrasives, suitable for polishing harder metals such as stainless steel and steel.
Green Buffing Compounds: These are used for high-gloss finishes on metals like nickel and chrome.
Abrasive Compounds: These compounds are used in the initial stages of the polishing process. They come in various grit sizes, ranging from coarse to fine, and help to remove surface imperfections, deep scratches, and oxidation. Abrasive compounds are typically applied during the grinding or sanding phase before the final polishing stages.
Ceramic Compounds: Ceramic finishing compounds are designed for high-performance polishing tasks. These compounds are often used for high-end applications such as in aerospace or automotive industries, where precision and a flawless finish are paramount.
2. How Finishing Compounds Work
Finishing compounds work by providing a mild abrasive action that removes microscopic imperfections from the metal surface, leaving behind a smooth, shiny, and reflective finish. When applied to polishing wheels or buffing pads, the compound’s abrasive particles interact with the metal, polishing and smoothing it until the desired level of shine is achieved.
In addition to their polishing properties, finishing compounds can also help protect the metal by adding a layer of wax or corrosion-resistant material. For example, some finishing compounds include ingredients that help prevent tarnishing or rusting, offering a protective coating that extends the life of the metal surface.
Choosing the Right Metal Polishing Equipment and Finishing Compounds
Selecting the right metal polishing equipment and finishing compounds largely depends on the type of metal you're working with, the desired finish, and the scale of the operation. For instance:
For small-scale applications like jewelry or decorative pieces, hand tools or bench polishing machines combined with a suitable polishing compound might suffice.
For larger, industrial-scale tasks, you might require heavy-duty polishing machines, vibratory tumblers, and high-performance finishing compounds to handle the volume and complexity of polishing large metal parts.
Conclusion
Metal polishing and finishing are critical processes in ensuring the quality and appearance of metal components, whether they are decorative pieces, automotive parts, or industrial machinery. Metal polishing equipment, including polishing machines, wheels, and rotary tools, combined with the right finishing compounds, can transform rough, dull surfaces into smooth, shiny, and corrosion-resistant metals. By selecting the appropriate tools and compounds for your specific needs, you can achieve exceptional results that enhance both the functionality and aesthetics of metal surfaces.
Write a comment ...