In the world of metalworking and manufacturing, achieving the perfect surface finish is often as crucial as the structural integrity of the material itself. This is where polishing and grinding machines, along with specialized metal cut and shine compounds, come into play. Together, they form a critical part of the finishing process, ensuring metals not only perform efficiently but also look flawless.
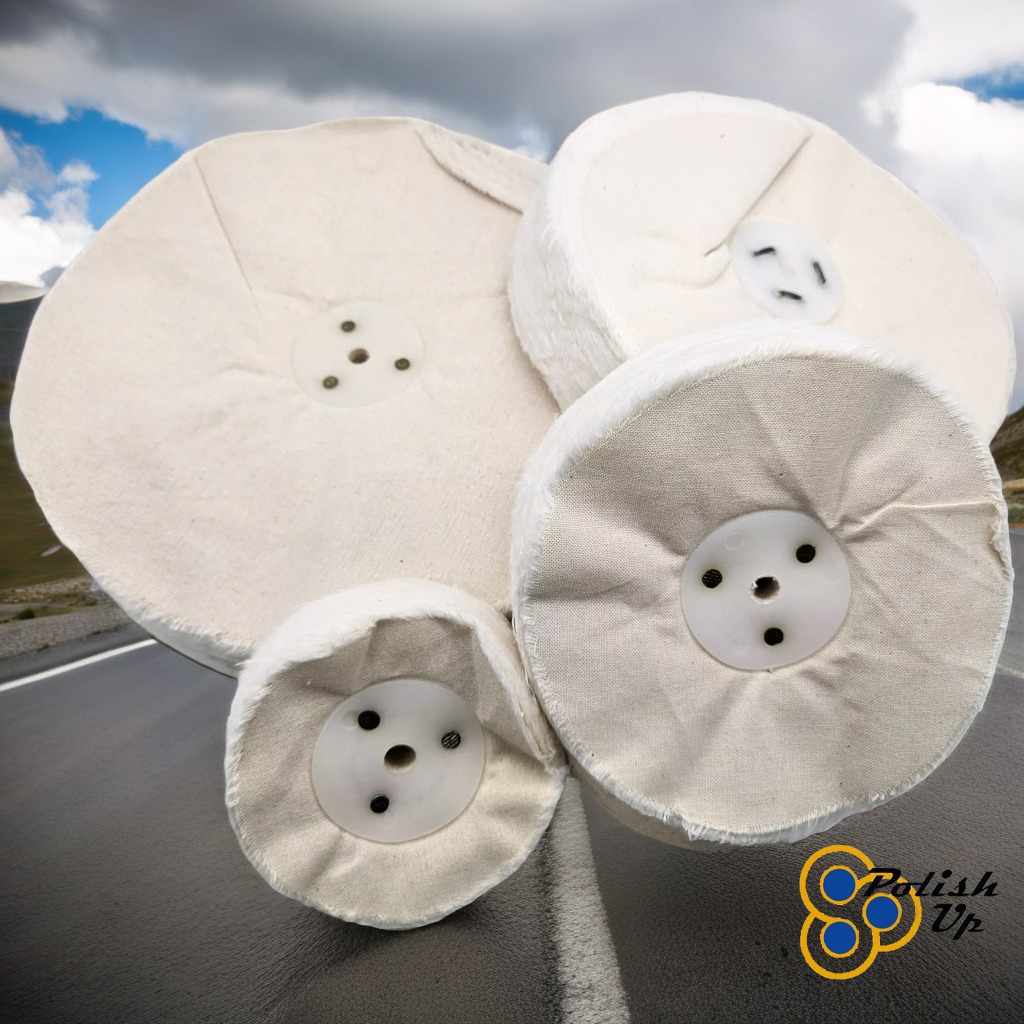
Polishing and grinding machine are versatile tools used across a variety of industries such as automotive, aerospace, construction, and even jewelry making. These machines are designed to smooth, shape, and refine metal surfaces through mechanical abrasion. Grinding machines typically use abrasive wheels to remove significant amounts of material from metal surfaces. This process is ideal for preparing materials for further machining or ensuring dimensional accuracy. On the other hand, polishing machines employ finer abrasives and compounds to remove only the surface irregularities and enhance the metal’s shine and smoothness.
The choice of machine and abrasive material depends largely on the type of metal being treated and the desired finish. For instance, stainless steel might require a different set of grinding wheels and polishing compounds compared to softer metals like aluminum or brass. Modern polishing and grinding machines often come with adjustable speeds, ergonomic controls, and dust collection systems, making them safer and more efficient to use. Automation and CNC integration in these machines have further revolutionized the industry by enabling precise, repeatable finishes on complex components.
While machines provide the mechanical action necessary for shaping and finishing, metal cut and shine compounds are equally important. These compounds are formulated with various abrasives and lubricants designed to work with specific metals. Cutting compounds are used during the initial stages of polishing. They contain coarser abrasives that help in removing scratches, oxidation, or welding marks. These are typically applied with polishing wheels or buffing pads and are essential for preparing the metal surface before fine polishing.
Shine compounds, often known as finishing or rouge compounds, are used in the final polishing stages. They contain finer abrasives that smooth out minor imperfections and bring out a mirror-like finish on the metal surface. The type of shine compound used can significantly affect the final look of the product. For example, a white rouge might be used for silver, while a green compound could be better suited for stainless steel.
Using the right combination of machines and compounds not only improves the aesthetic appeal of the metal but also enhances its resistance to corrosion and wear. A well-polished surface has fewer microscopic crevices where dirt and moisture can accumulate, which is especially important in industries like food processing or medical equipment manufacturing where hygiene is paramount.
In addition to their functional benefits, polished metal surfaces also carry a high visual appeal, which is why polishing is a common practice in decorative and architectural metalwork. Whether it's the gleaming surface of a luxury car’s chrome trim or the smooth finish of a stainless steel kitchen appliance, the impact of a properly polished surface is undeniable.
In summary, polishing and grinding machines, paired with the correct metal cut and shine compounds, are essential tools in modern manufacturing and craftsmanship. They enable professionals to achieve the desired finish and functionality for their metal components. As technology continues to evolve, so too do the tools and techniques for metal finishing, promising even greater precision, efficiency, and aesthetic possibilities.
Write a comment ...