In the world of metalworking and fabrication, achieving the perfect finish is not just a matter of aesthetics—it's often essential for functionality, safety, and quality. Whether you're working on industrial components, jewelry, automotive parts, or custom metalwork, the tools you use to polish and grind make all the difference. Two standout essentials in this field are the barrel polisher grinder machine and metal polishing wheels. Together, they form a powerful combination for transforming raw or rough materials into smooth, gleaming, and professionally finished pieces.
A barrel polisher grinder machine, often simply referred to as a barrel polisher or tumbler, is a powerful and versatile tool designed for polishing and deburring small to medium-sized metal parts. This machine operates by rotating a barrel filled with abrasive media and the workpieces. As the barrel turns, the constant movement and friction between the media and the metal items gradually smooth out rough edges, remove surface imperfections, and produce a polished finish. It's an automated, time-efficient process that allows for uniform results across large batches of parts.
Barrel polishers are especially valuable in industries where precision and presentation matter. Jewelers, for instance, rely on these machines to bring out the brilliance in rings, bracelets, and pendants. Manufacturers use them to deburr machined parts, ensuring smooth operation and preventing damage caused by sharp edges or burrs. These machines can handle a wide range of materials, including stainless steel, brass, aluminum, and even certain plastics, making them an integral part of many workshop operations.
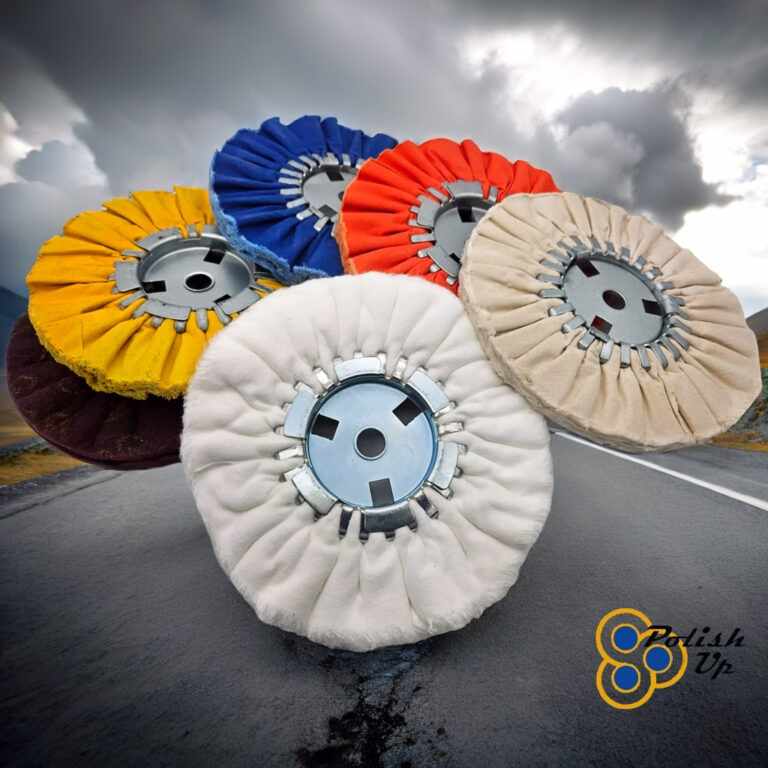
The key to a barrel polisher’s effectiveness lies in the combination of the right media, speed, and duration. Abrasive media comes in various shapes and compositions—ceramic, plastic, or stainless steel—and each serves a unique purpose, from heavy grinding to fine polishing. The operator can customize the process based on the type of finish desired, making barrel polishers highly adaptable for different applications.
While barrel polishing machines are great for batch processing, metal polishing wheels are indispensable when it comes to hands-on, detailed work. These wheels are used with bench grinders, angle grinders, or handheld polishing machines to refine and shine individual pieces with precision. They come in a variety of types and materials, each designed for specific tasks in the metal finishing process.
Felt wheels, sisal wheels, and cotton buffs are commonly used in metal polishing. Each type offers unique advantages: felt wheels are ideal for applying polishing compounds and achieving a mirror finish, while sisal wheels provide a more aggressive action for initial buffing and cutting through oxidation or scale. Cotton buffs are perfect for final finishing, delivering a high-gloss shine that brings out the natural luster of metals.
Polishing wheels are used extensively in industries ranging from automotive restoration to custom metal fabrication. They help in achieving smooth, rust-free surfaces that not only look better but also resist corrosion and wear. In fabrication shops, these wheels are often used to prepare metal surfaces for welding or painting, ensuring better adhesion and longer-lasting results.
One of the great advantages of modern metal polishing wheels is their compatibility with various polishing compounds. These compounds, available in bars or pastes, contain fine abrasives that enhance the cutting or polishing action of the wheels. Whether you’re working with chrome, stainless steel, copper, or aluminum, there’s a combination of wheel and compound designed to deliver optimal results.
Both barrel polisher grinder machines and metal polishing wheels are essential in creating the flawless finishes demanded by today’s high standards in manufacturing and design. When used together, they offer both efficiency and precision—barrel polishers for bulk finishing and polishing wheels for detailed, high-touch refinement.
Investing in the right polishing equipment is not just about surface appearance—it’s about performance, longevity, and customer satisfaction. Whether in a high-volume workshop or a precision-focused studio, these tools ensure that every piece, large or small, meets the mark with brilliance.
Write a comment ...