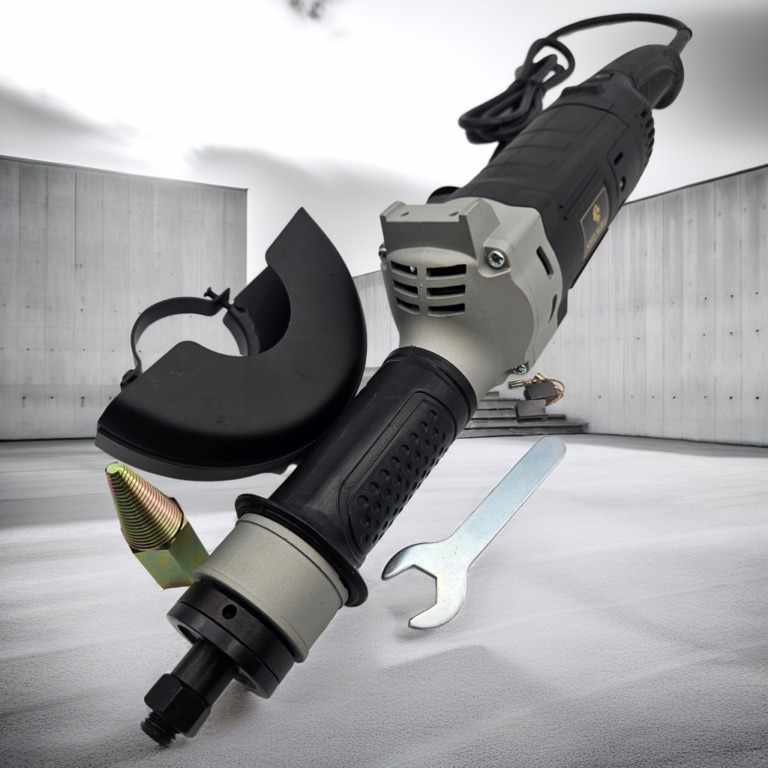
When it comes to creating a flawless, reflective finish on metal surfaces, the combination of high-quality metal cut and shine compounds with efficient metal polishing machines plays a vital role. These tools are the backbone of a wide range of industries, from automotive and aerospace to jewelry making and sculpture. Let’s dive into the world of metal finishing and understand how these essential components work together to achieve a perfect shine.
What Are Metal Cut and Shine Compounds?
Metal cut and shine compounds are specialized products designed to smooth, cut, and polish metal surfaces to achieve a high-gloss, smooth finish. These compounds are formulated with abrasive materials that help to remove imperfections, scratches, and oxidation while enhancing the natural shine of the metal. They are essential in the metalworking industry, where precision and aesthetic appeal are equally important.
Metal Cut Compounds: Cutting compounds are typically used in the initial stages of metal polishing. Their main function is to remove heavy scratches, imperfections, and surface blemishes. These compounds contain coarse abrasives that help to level out rough surfaces, making them smooth and ready for further finishing. Metal cut compounds are ideal for tasks such as grinding and sanding, where deep marks or oxidation need to be removed efficiently.
Metal Shine Compounds: Shine compounds are used after the cutting process to refine the surface and enhance its reflective properties. These compounds are generally finer in texture and designed to remove the small scratches and marks left behind after the cutting process. Shine compounds are perfect for achieving that mirror-like finish that is highly desired in metalwork, giving the metal a sleek, polished, and high-gloss appearance.
The combination of cut and shine compounds helps achieve a smooth, even finish, ensuring the metal is not only visually appealing but also resistant to corrosion and wear.
Metal Polishing Machines: The Power Behind the Shine
Metal polishing machines are essential tools that automate and optimize the process of polishing and finishing metal surfaces. These machines come in various shapes and sizes, designed for different types of metalworking tasks. Whether you are polishing small metal parts or large components, the right polishing machine makes all the difference in achieving a consistent and high-quality finish.
1. Bench Polishing Machines: Ideal for small parts and intricate details, bench polishing machines feature a rotating spindle where polishing wheels and compounds are mounted. These machines are perfect for tasks such as jewelry polishing, small automotive parts, and decorative items. With adjustable speeds and a variety of polishing wheels, they can deliver the precision needed for fine finishes.
2. Rotary Polishing Machines: Rotary polishing machines are used for larger metal parts and are commonly found in the automotive, industrial, and aerospace sectors. These machines feature a rotating wheel that works in tandem with cut and shine compounds, allowing for a powerful yet smooth polishing action. The ability to adjust speed and pressure gives operators more control over the polishing process, ensuring optimal results.
3. Vibratory Polishing Machines: Vibratory polishing machines are ideal for finishing large batches of smaller parts, offering an efficient way to polish items such as fasteners, bolts, and components that require uniform shine. The machine uses a vibratory motion to agitate both the parts and the polishing media, which works with the compounds to smooth and shine the surface.
4. Orbital Polishing Machines: Orbital polishers are designed to provide an even, swirl-free finish on metal surfaces. These machines are particularly useful in applications where a high-gloss finish is required without creating visible swirl marks. Their unique orbital motion ensures consistent results without causing any damage to the metal surface.
The Process of Metal Polishing
The metal polishing process typically follows these steps:
Preparation: The metal surface is first cleaned to remove any dirt, grease, or debris that might interfere with the polishing process.
Cutting: The metal cut compound is applied to the surface to remove deep imperfections, scratches, and oxidation.
Shining: After the surface is leveled, shine compounds are used to refine the finish, removing finer scratches and producing a polished surface.
Finishing: The metal is buffed with a polishing machine to achieve the desired high-gloss shine.
Choosing the Right Metal Cut and Shine Compounds & Polishing Machines
Selecting the right cut and shine compounds and polishing machines depends on the specific metal, the desired finish, and the scale of the project. Here are some tips to help you make the right choice:
Consider the Material: Different metals, such as aluminum, steel, brass, or copper, require different types of compounds and machines. Always choose products designed specifically for the material you are working with.
Assess the Desired Finish: If you are aiming for a high-gloss, mirror-like finish, fine-cut compounds and orbital or rotary polishing machines are ideal. For heavy-duty surface correction, a stronger cut compound may be necessary.
Machine Size and Power: Choose a polishing machine that fits the size of your workpieces. Larger machines are better suited for industrial applications, while smaller machines are more appropriate for intricate or small-scale projects.
Conclusion
Metal cut and shine compounds, paired with the right metal polishing machines, are key to achieving a flawless finish in metalworking. Whether you’re working on small jewelry pieces or large industrial components, these tools ensure that your metal surfaces are not only smooth and polished but also durable and resistant to wear. With the proper technique, equipment, and compounds, you can master the art of metal finishing and achieve results that shine.
Write a comment ...